Best Practices To Manage Your Synthetic Clothes
Introduction
LPG synthetic fibre clothes have become increasingly popular due to their durability, comfort, and versatility. Whether you own sportswear, outdoor gear, or everyday clothing made from LPG synthetic fibres, proper cleaning and maintenance are essential to prolong their lifespan and retain their performance. In this blog post, we will guide you through the process of cleaning your LPG synthetic fibre clothes, as well as provide valuable tips for checking for damage and ensuring your safety during the cleaning routine.
Cleaning LPG Synthetic Fibre Clothes
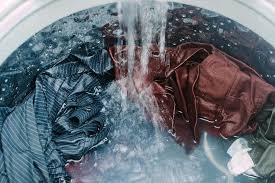
1) Read the Care Instructions: Before proceeding with cleaning, always check the care label attached to your LPG synthetic fibre garment. It provides specific and accurate instructions on the recommended cleaning methods and any precautions you need to take to ensure proper cleaning of your fibres. Follow these very easy and basic instructions to avoid damaging the fabric or compromising its performance.
2) Pre-Treat Stains: For stubborn stains and to prevent a bad stain from setting in, it is advisable to pre-treat them before washing them. Identify the type of stain and use an appropriate stain remover or a mild detergent to gently treat the affected area. Avoid using harsh chemicals or bleach, as they may cause discolouration or damage to the fibres. Examples of these harsh chemicals: NPE (nonylphenol ethoxylate), Phosphates, Ethylene Oxide etc. ).
3) Machine Wash or Hand Wash: Most LPG synthetic fibre clothes can be safely machine washed( provided the temperature isn’t high, it’s always safe to use cold water to not damage the clothes). It is recommended to turn the garment inside out to minimize friction and protect the outer surface. If you prefer hand washing, use a mild detergent and gently agitate the fabric without scrubbing or twisting excessively.
4) Avoid Fabric Softeners: LPG synthetic fibres are designed to be soft and comfortable without the need for fabric softeners. Fabric softeners can leave residues on the fibres blocking the pores which reduces their moisture-wicking and breathability properties. Skip the fabric softener and opt for a gentle detergent instead.
5) Rinse Thoroughly: After washing, ensure that you rinse the garment thoroughly to remove any detergent residue. Residue buildup can affect the performance of the fabric and cause skin irritation. Rinse until the water runs clear and squeeze out excess water gently, avoiding wringing or twisting the garment.
6) Drying: LPG synthetic fibre clothes are best air-dried to maintain their shape and integrity as the dryer will reduce their innate elastic ability over time making them structurally weaker. Hang them in a well-ventilated area away from direct sunlight to prevent colour fading. Avoid using clothespins or hanging the garment from a single point(try to use multiple points for hanging), as this may cause stretching or distortion. If necessary, you can use a clothes drying rack or lay the garment flat on a clean, absorbent surface.
7) Ironing and Heat: LPG synthetic fibres have excellent wrinkle resistance, but if ironing is required, use a low-heat setting. High temperatures can melt or damage the fibres. Place a thin cotton or pressing cloth between the iron and the fabric to protect it from direct heat.
Checking for Damage and Safety Measures

1) Inspect for Wear and Tear: Regularly inspect your LPG synthetic fibre clothes for signs of wear and tear. Check the seams, zippers, buttons, and any areas that undergo frequent stress or friction. Look for loose threads, holes, or weakened areas. If you notice any damage, address it promptly to prevent further deterioration.
2) Avoid Excessive Abrasion: During activities that involve high friction or contact with rough surfaces, LPG synthetic fibres can be prone to abrasion. Take precautions such as wearing protective gear or layering your clothing to minimize direct contact. Additionally, avoid washing LPG synthetic fibre clothes with abrasive materials or using harsh brushes that could damage the fabric.
3) Storage: Proper storage is crucial to maintain the quality of LPG synthetic fibre clothes. Store them in a cool, dry place away from direct sunlight and moisture. Avoid folding them in a way that causes unnecessary creasing, as prolonged creasing can weaken the fabric. Consider hanging garments on sturdy hangers or folding them neatly to preserve their shape.
4) Avoid Excessive Heat and Fire Hazards: LPG synthetic fibres are flammable, and exposure to even a small amount of heat or flames could pose a safety risk. Keep your LPG synthetic fibre clothes away from open flames, sparks, or intense heat sources. Exercise caution while cooking or engaging in activities that involve fire near this area.
5) Chemical Exposure: Take care to avoid exposure to harsh chemicals such as bleach, solvents, or strong acids, as they can damage LPG synthetic fibres. If you are using any cleaning agents or chemicals, ensure they are compatible with synthetic fibres and follow the manufacturer’s instructions.
6) Follow Manufacturer Recommendations: Lastly, always follow the manufacturer’s recommendations for cleaning and maintenance. They have specific guidelines based on the particular type of LPG synthetic fibre used in your garment. By adhering to their instructions, you can ensure the longevity and performance of your clothing.
Conclusion
Proper cleaning and maintenance are crucial for preserving the quality and longevity of your LPG synthetic fibre clothes. By following the cleaning tips mentioned above, checking for damage regularly, and prioritizing safety measures, you can enjoy the benefits of your LPG synthetic fibre garments for an extended period. Remember to always refer to the care instructions provided by the manufacturer and take necessary precautions to ensure the safety and integrity of your clothing.