How was it done before?
1) Forging
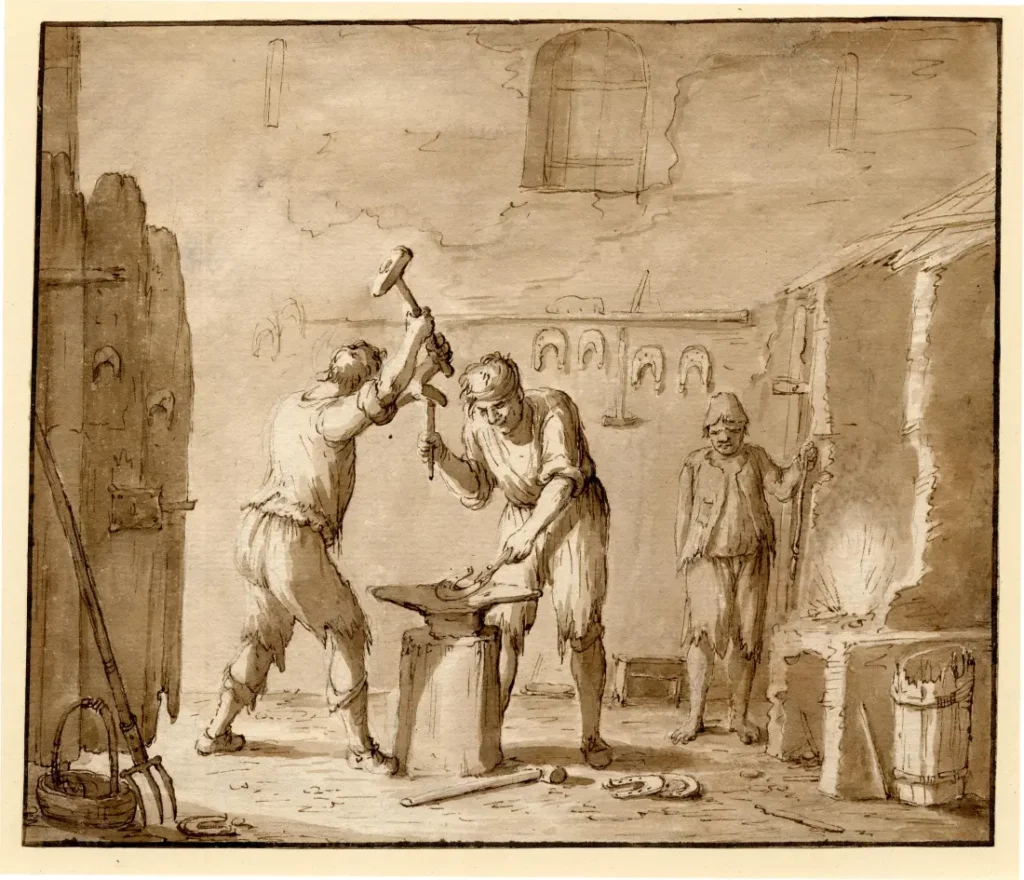
Forging is one of the oldest metalworking techniques known to mankind. It involves heating the metal until it becomes malleable and then shaping it using hammers or anvils. This further allowed blacksmiths to create a variety of complex shapes and join pieces of metal together through techniques such as riveting or forge welding.
The forging process during this early period typically involved heating the metal in a fire and then hammering it with a stone or metal hammer while it was hot and the metal undergoes a phase called “recrystallization” when it is hot allowing for it to retain any shape it is forced into when heated. This metal was heated in a simple charcoal or wood fire, and the hammering was done on a hard and stable surface, such as a rock or an anvil made of stone or bronze.
During this time, humans used to work with metals like copper, bronze, and iron, and the people who did this work were called blacksmiths. These blacksmiths likely used simple tools such as tongs, hammers, and anvils to shape the metal. They may have also used molds made from clay or sand to create specific shapes.
The practice of forging metals predates written records and can be traced back to prehistoric times. Archaeological evidence suggests that early human civilizations were working with metals and employing forging techniques even before the invention of writing.
2) Riveting
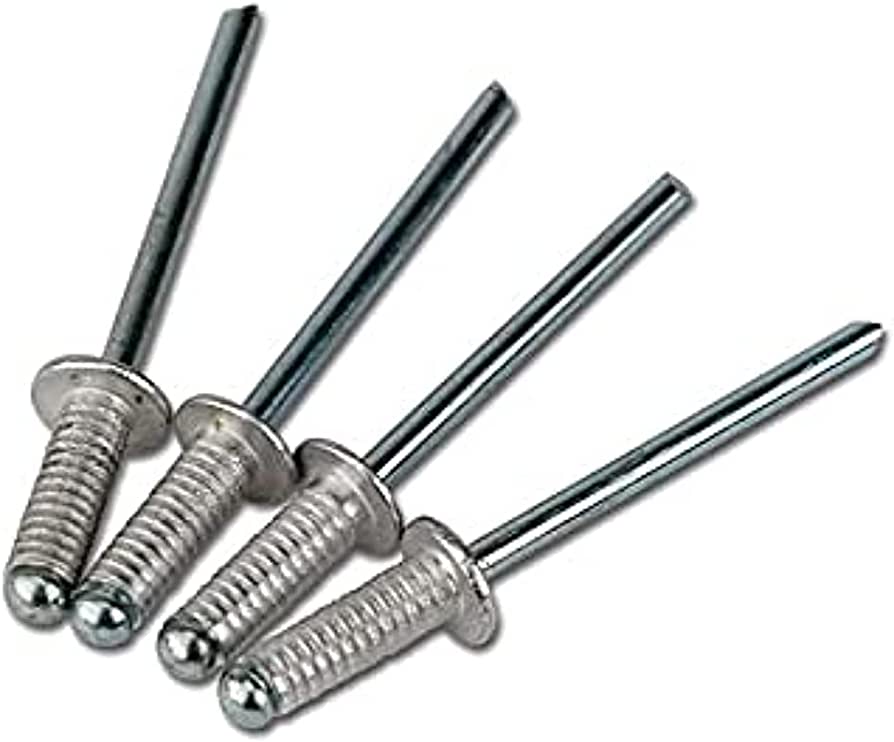
Riveting was a common method of joining metal parts before welding became prevalent. It involved drilling holes in the metal pieces and inserting a hot rivet through the holes (A rivet is a type of permanent mechanical fastener used to join two or more pieces of material together. It consists of a cylindrical shaft with a head on one end). The rivet was then hammered to flatten it on both ends, creating a much more permanent connection between the metal pieces.
Riveting as a method of fastening has been used for thousands of years, with its origins dating back to ancient times. The exact timeframe when riveting started is difficult to determine, as it predates written records. However, evidence suggests that riveting was used in various civilizations throughout history.
Ancient civilizations such as the Egyptians, Greeks, and Romans employed riveting techniques in their construction projects. For example, the construction of ancient Egyptian chariots involved the use of rivets to join metal components together. Roman engineers used riveting to assemble large structures like bridges and aqueducts.
In ancient times, riveting was done by heating the rivet until it was red hot and then placing it through a pre-drilled hole in the materials to be joined. The rivet was then held in place with a pair of tongs, while a second person used a hammer or another tool to deform the end of the rivet, creating a permanent joint. This process is called “hot riveting.”
What do we do right now?
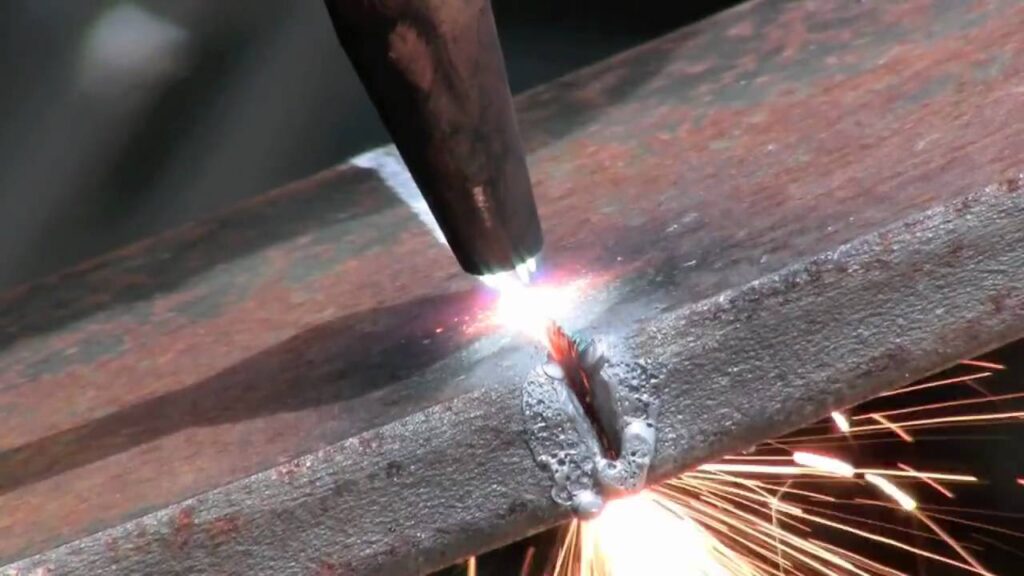
Currently, metalworking such as welding and cutting of metals involves the use of LPG (liquefied petroleum gas), specifically, it is used in oxy-fuel welding and cutting. Oxy-fuel welding involves using a fuel gas, such as LPG, in combination with oxygen to produce a high-temperature flame of about 3,000 to 3,500 degrees Celsius for welding and about 2,800 to 3,200 degrees Celsius for cutting.
In this process, LPG acts as the fuel source for the welder or cutter equipment, while oxygen is the oxidizing agent. The LPG and oxygen gases are mixed and ignited at the cutting nozzle, resulting in a focused and high-temperature flame. The intense heat from the LPG-oxygen flame rapidly oxidizes and melts the metal being cut. Simultaneously, a jet of high-pressure oxygen is directed onto the heated metal, blowing away the molten metal and creating a cut or groove.
It’s important to note that due to the high temperature proper safety precautions, such as adequate ventilation, protective gear, and adherence to guidelines, should be followed when using oxy-fuel welders or cutters.